Chemical recycling of PET – a new heterogeneous catalytic route
Project Director: Dr. Neatu Florentina
Project ID:
PN-III-P1-1.1-TE-2019-1969/ RECYCLE
Project coordinator: Dr. Florentina Neațu
Project type: National
Project Program: TE
Funded by: Romanian National Authority for Scientific Research, UEFISCDI
Contractor: National Institute of Materials Physics
Project Status: Finalized
Start date: 01.09.2020
End date: 31.10.2022
Plastic is an essential material in our daily lives that has multiple functions: food packaging bottles and jars, insulators, microchips in phones and computers, textile industry and so on. The world’s annual consumption of plastic materials has increased from around 5 million tonnes in the ‘50s to nearly 300 million tonnes in 2020. Due to plastic’s resistance against degradation and its increased production in industry, the issue of plastic pollution has evolved to become a menace to global ecology. Therefore, there is an urgent need to resolve these environmental issues that minimise the importance of these materials that play an important role in our daily lives. All these recycling approaches have limitations because the PET can only undergo a finite number of processing cycles before their properties are significantly compromised ends up in the landfills or is incineration, being the source of others pollutants. However, PET could be recovered through chemical recycling, we could save the natural resources and the prices of polymers would be lower. RECYCLE propose a simple solution, to heterogeneously catalyse PET depolymerisation using surface modified flexible materials, in which 2D malleable flakes/sheets are surface modified by strong acidic functionalities, like sulfonates.
Project coordinator: Phd. Florentina Neatu -- Senior researcher I
Members:
Phd Mihaela Florea - Senior researcher I
Phd Mihaela Mirela Trandafir - Senior researcher
Phd Andrei Kuncser - Senior researcher III
Phd Mahesh Nair - Assistent researcher
Phd student Andrei Tomulescu - Assistent researcher
Stage I - 2020
Preparation of 2D material containing Ti, Fe, Mn, Nb and Zr.
In this short (3 months) phase only one activity was foreseen: the synthesis of simple MXene by the simplified method, containing the following elements: Ti, Mn, Fe, Zr and Nb.
For the synthesis of Me2C precursors of the selected metals and glucose as carbon source were used, in a specific molar ratio, in a well-defined amount of distilled water. To ensure homogeneity of the solution at moderate temperature, the precursors were added under magnetic stirring at room temperature. The mixture was subjected to hydrothermal treatment, at moderate temperature after which it was recovered by filtration and washed. The materials were subjected to high temperature heat treatment in an inert atmosphere.
Examples of materials during synthesis are shown in the Figure below.
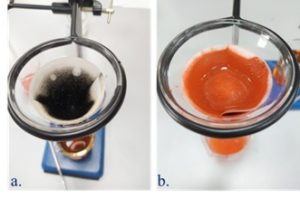
Mn2C and Fe2C after hydrothermal treatment
All the objectives were fully performed. The synthetic scientific report in .pdf format is available at the contracting unit.
Stage II - 2021
Preparation and characterization of solid acid catalysts
A number of double MXenes were successfully prepared and further modified with -SO3H groups. These materials were tested in PET depolymerization and proved to be effective in achieving catalytic depolymerization to the feedstock stage.
Synthesis of double MXene by modified method - 3D MAX layered carbide-phases with the molecular formulae Ti3SiC2 and Ti3AlC2 were used in etching reactions with the aim to remove the A-type element, silicon and aluminium, from the system using in situ generated hydrofluoric acid. The optimization step of the MXenelor preparation process involved changing the concentration of the acid solution used. X-ray diffraction revealed theappearance of a diffraction peak at smaller angles corresponding to the (002) crystal plane, identifying the 2D structure as the major phase. Acidity was introduced into the materials by two different methods, one of which was effective.
The materials were characterized by different techniques such as TEM and SEM to verify the 2D structure of the materials. XRD characterization was used as a complement to the two techniques mentioned before to confirm the 2D structure of the materials. The acidity of the materials was performed using the DRIFT-NH3 technique, where grafting of acid groups onto the surface of the prepared materials was confirmed.
Screening of the materials prepared in the previous activities was performed for the depolymerization reaction of PET. Different parameters were varied, such as solvent, temperature or reaction time Some of the materials proved to be efficient for this reaction, obtaining the desired compounds in a high yield (Figure).
The objectives were fully met. The detailed results can be found in the scientific report submitted to the contracting authority.
Stage III - 2022
Characterisation and correlation of results for PET depolymerisation
In this stage the aim was to optimise reaction conditions and establish correlations between catalyst properties and catalytic activity.
Given the relatively low presence of sulphur on the surface of 2D layered carbide materials observed from the morpho-structural characterisations using techniques such as XPS or STEM/EDS for the materials prepared in the previous stage, the first step to optimise the synthesis was to increase the amount of acidic groups threefold and fivefold.
The obtained materials were further tested in PET depolymerization reactions for comparative study with the results obtained with the original catalyst (under the same reaction conditions). Both the conversions obtained and the yields in the product of interest increase with increasing amount of acidic groups of the catalyst. Another working hypothesis was to double the amount of catalyst in the reaction and keep the other parameters constant.
The catalyst with the highest amount of acidic groups was tested at several reaction temperatures, 160-180 °C for comparative study of the results obtained. At the same time, several types of PET were tested in the depolymerization catalytic reactions (Figure), given the many forms in which it is found in waste, namely a) PET from a transparent bottle; b) PET from a white 100% polyester T-shirt and c) PET from a green bottle. Comparing the three types of PET used in the reactions, the best substrate conversion and yield results in the product of interest are obtained for PET from clear plastic bottle.
The objectives were fully met. The detailed results can be found in the scientific report submitted to the contracting authority.
In this project all the proposed objectives of the project have been fully achieved. The depolymerization of PET was achieved with formation of terephthalic acid and ethylene glycol, which is more than the BHET intermediate (proposed in the project). This represents an important step for this reaction and for the chemical depolymerisation of polyethylene terephthalate in general, which consequently has an important economic and social impact on the reuse of PET, an important source of pollution.
5. 8th EuChemS Congress 2022, 27 august - 3 September 2022, Lisabona, Portugalia “Selective etching of MAX phases to MXenes and different synthesis methods to increase surface acidity”, Iuliana M. Chirica, Ștefan Neațu, Anca Mirea, Michel W. Barsoum, Mihaela Florea, Florentina Neațu; (poster).
6. 8th EuChemS Congress 2022, 27 August - 3 September 2022, Lisabona, Portugalia “Sulfonated MXenes as efficient catalysts for PET depolymerization”, Iuliana M. Chirica, Ștefan Neațu, Anca Mirea, Michel W. Barsoum, Mihaela Florea, Florentina Neațu; (poster).
7. 2nd international MXene conference at Drexel University, 1-3 August 2022, Philadelphia, USA, “PET catalytic depolymerization by MXene-SO3H modified materials“, Florentina Neaţu, Iuliana M. Chirica, Ștefan Neațu, Anca Mirea, Michel W. Barsoum, Mihaela Florea; (poster).
PROJECTS/ NATIONAL PROJECTS
Copyright © 2025 National Institute of Materials Physics. All Rights Reserved